WANTED!
MACHINE FOR SOPHISTICATED
FINISHING OF PLASTICS
Found: 5-axis CNC gantry milling machine from HG Grimme SysTech
Krüger Aviation urgently required a machine for finishing plastics. The company from northern Germany then found the 5-axis CNC gantry milling machine from HG Grimme SysTech.
(Author: Nikolaus Fecht, technology journalist)
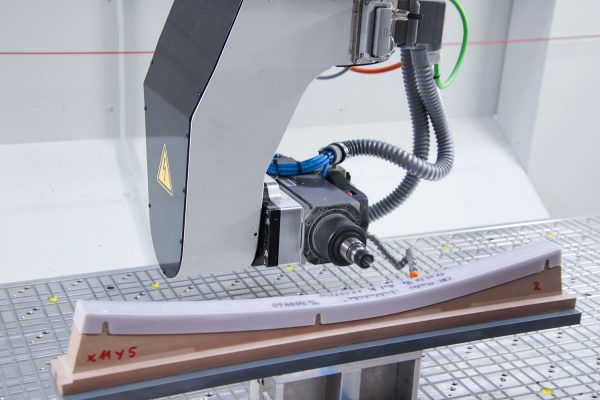
High demands for finishing plastics
When the long-established company Krüger Aviation needed a machine for finishing plastics at short notice, satisfying the high demands was therefore a very big challenge. For it is no accident that Krüger Aviation GmbH from Barsbüttel near Hamburg boasts a list of references that reads like a who’s who of the aviation industry: The long-established Hanseatic company supplies more than 300 companies in the industry – from Airbus, Lufthansa Technik, Safran through to ZIM Flugsitz. Customers like these definitely expect their suppliers to use the very best machinery and processes – including when finishing plastics.
Trend: Switching from aluminium to plastic
The supreme quality that Krüger Aviation GmbH provides is of course not just down to the machines that are used but also the 40 employees who apply processes including thermoforming, CNC machining and 3D printing to manufacture semi-finished products as well as complex finished parts and assemblies from plastic. “We also help our customers to design and certify components or even switch from one production process to another,” explains Florian Ehinger, Head of Customer Service. “But increasingly customers are coming to us with an aluminium component and asking: Could you suggest to us a plastic that we could maybe use instead of aluminium here?”
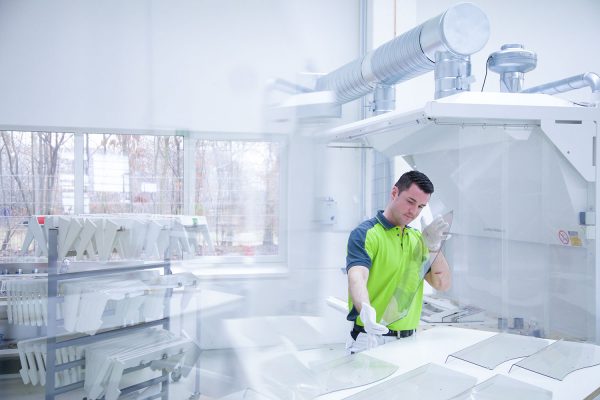
Visual quality plays an important role
The company’s particular specialities include high-quality mirrors made from special plastic. The firm from northern Germany is one of the world’s leading suppliers of this product and has already received multiple awards such as the Crystal Cabin Award. The factory in Barsbüttel also uses thermoforming to make light and seat fitting covers as well as other components for use in cabin and toilet areas from materials including polycarbonate (PC), polyamide (PA 66) or polyphenylsulfone (PPSU).
But all components have one thing in common: They are visible parts without any supporting function. Ehinger: “Visual quality plays an important role with all our components. This is why we make a very big effort here.”
Just-in-time delivery is another requirement: The aviation industry insists on extremely short delivery times even for the components that are usually customised and made in small batches. This is why Krüger Aviation optimises all processes from development and production through to handling.
Where can you find machines for finishing plastics?
But back to the original question: What does a long-established, fourth-generation company with a history stretching back more than 100 years do when it suddenly requires a milling machine that is both highly precise and extremely fast for machining plastic deep-drawn parts for what is known as trimming?
Initially the company based in northern Germany carefully examined the machines from well-known local companies, but then it came across HG Grimme SysTech GmbH from Wiedergeltingen in the southern Unterallgäu district. An advantage of HG Grimme is that, just like Krüger Aviation, it is a family-run, medium-sized enterprise. It has also specialised in a high-tech niche area of plastics processing. Since as far back as the 1980s, it has been manufacturing CNC machining centres for finishing deep-drawn parts, which was rare in Germany at the time. The Bavarian company has also been making CNC gantry machining centres since 2010.
5-axis CNC gantry milling machine
But it was not just the expertise in plastics processing and the support provided in partnership that impressed the powers-that-be. “HG Grimmes’ performance potential for our form of plastics finishing is ideal for us,” says Ingo Horster, Chief Technical Officer (CTO) at Krüger Aviation. “And then there was also a 5-axis CNC gantry milling machine whose compact size and performance was the perfect fit. HG Grimme made just a few minor adjustments to the demonstration machine. And very quickly we were able to start trimming deep-drawn parts.”
Solid vacuum clamping table wanted
The phrase “minor adjustments” probably reflects Hanseatic understatement because Krüger Aviation had a specific request: The workpiece holder which the northern German company developed was a vacuum clamping table which, together with semi-finished products, can even hold complex shaped components at a high milling speed securely and without any vibrations. The vacuum clamping table which was developed in-house was previously made of wood or Ureol. HG Grimme was now given the task of producing a solid aluminium version. The desire to have an even more robust clamping table is understandable given that the new gantry design machines in the X/Y axis at a speed of up to 80 metres per minute.
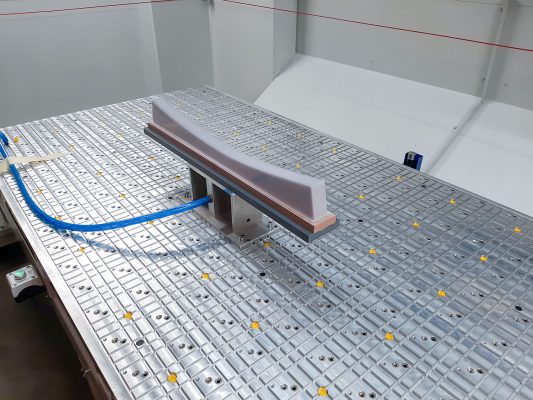
Dynamic machining with a milling head mounted on one side
An unusual sight for experts in metalworking is the very compact milling head which can rotate up to a maximum of 540 degrees and can tilt up to 365 degrees. “As the sort of high forces that are common in metalworking do not occur here, we can operate with a milling head mounted on one side,” explains Horster. “We can also use it to mill the typically intricate workpieces very dynamically because we can now tilt the head down a very long way without running the risk of the milling head colliding with the table or the holders.” The risk of collision is now much lower than it was with the previous machine.
The results with the first milled components were very good. Krüger Aviation started off with semi-finished thermoformed parts made from the plastic Ureol and is now also testing components made from other plastics for the aviation industry for which the first article inspection by the customers is now pending.
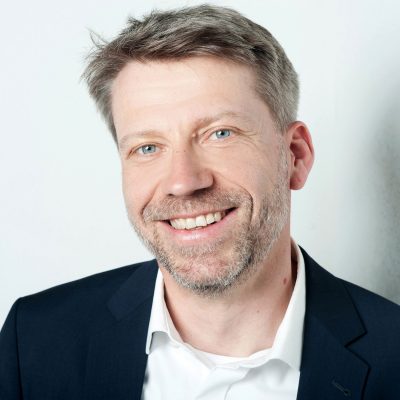
“So far everything has worked brilliantly. Although we are not timing every milling process with a stopwatch, it is definitely the case that the cycle time for each workpiece has been halved.”
Ingo Horster, Chief Technical Officer (CTO) at Krüger Aviation | Picture: Krüger Aviation