5-axis rotary table milling machines
from HG GRIMME SysTech
deployed at DR FISCHER
Hard work all round in Overath
The quality of plastic components depends very much on the mechanical finishing. This is why for more than three decades Dr. Karl Gert Fischer GmbH & Co. KG, a leading company in the field of plastic thermoformed parts based in the Greater Cologne area, has relied on machine tools from HG GRIMME SysTech from Germany’s Allgäu region. What is remarkable is that the company primarily uses rotary table machines – which is a rare thing in this industry.
“This story is a typical example that demonstrates the ingenuity of the Bergisches Land region,” says Dr. Ingo Gehlhaar, customer adviser at HG GRIMME SysTech GmbH in Wiedergeltingen (Unterallgäu). “It all starts with spotting a gap in the market, followed by constant tinkering before ultimately finding a solution that is then constantly optimised.”
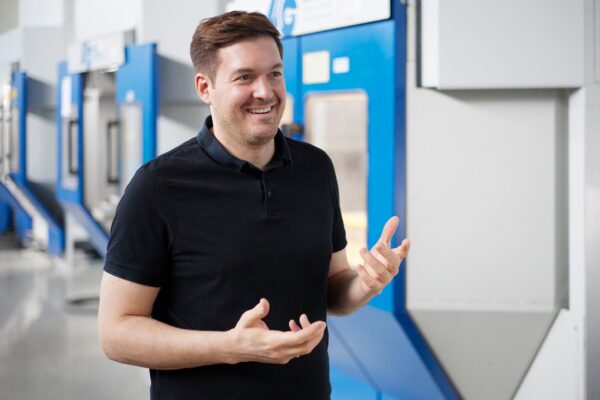
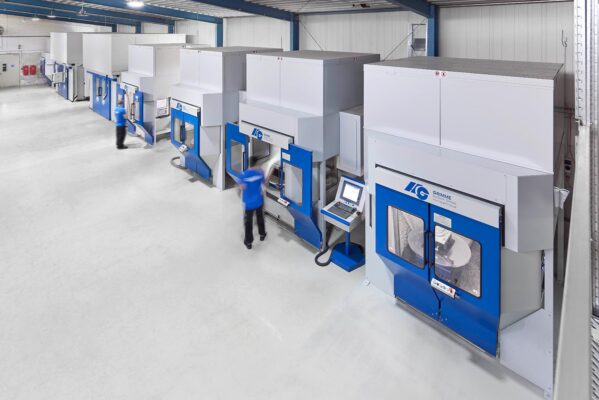
Gap spotted: There’s a lack of control cabinets made of plastic
The gap was identified by Dr. Karl Gert Fischer in the 1970s while he was working for a shipbuilder: There were no companies that were making corrosion-resistant plastic control cabinets with good electrical insulation for ships. Spurred on by this discovery, the engineer with a doctorate in mechanical engineering founded a small company in Cologne that initially manufactured control cabinet components for his former employer.
Dr. Karl Gert Fischer GmbH & Co. KG developed to become one of the leading suppliers of industrial thermoformed parts. From its present-day headquarters in Overath-Immekeppel (near Cologne), the family company, which is now managed by the second generation, can reflect on a real success story: It has managed to expand its production capacity significantly and now caters for lots of different sectors, especially machine construction and the commercial vehicle sector.
“Thermoforming has developed positively over the years and we’ve been able to place ourselves in a good position in this growing market,” explains managing director Constantin Fischer, son of the company’s founder. “The thermoforming process and CNC milling cover a wide range of products.”
Digital transformation versus complexity
Digitisation delivered an additional boost. The company manufactures products for lots of customers, typically in batches of from 100 to 1000 components. “We’re expanding as our number of customers increases,” explains Fischer. “This is making our processes increasingly complex.” Without a powerful ERP system and simulation software for production planning, we would no longer be able to manage this level of complexity efficiently – especially for assemblies that can comprise up to 150 individual parts.
Fair play is another secret to the company’s success: The company founder really valued fair partnerships over a long period of time. “It’s vital to be fair to one another in both good and tough times,” stresses his son Constantin. This philosophy proved to be really valuable during the coronavirus pandemic in particular.
Long-lasting, fair partnerships also play an important role when dealing with suppliers. “We like to build long-term relationships with our suppliers,” says the managing director. The level of service is particularly commendable. “If there’s a crash, HG GRIMME helps us quickly without any fuss. The prices of spare parts and labour charges are reasonable.”
A fair partnership for more than three decades
Since 1992, the company has ordered a total of twelve machines from the Allgäu. Eight machines are currently in use; four of them were sold as second-hand machines. “We’re working at full capacity and this is why we regularly exchange our production machines for new models – we’ve done this every one or two years on average in the last decade. This means we can always stay right up to date with the latest technology,” says Fischer.
The machines from HG GRIMME have proven their worth: Whereas sawing and conventional milling processes used to be employed, 5-axis simultaneous milling revolutionised machining from the 1990s onwards. It improved the level of quality and sped up the machining processes. Gantry machines from the G-S-F series with a single-axis and dual-axis swivel head for larger components and rotary table machines from the R-TF 1400 series with a single-axis swivel head and rotary axis in the table are employed in Overath. The R-TF machines are equipped with a fast spindle (rotational speed: 40,000 min-1), tool changer, NUM control and light barrier in the gate area.
But why are six of the total of eight HG GRIMME machines rotary table machines? “We use them to operate multiple machines so we can make our production as efficient as possible,” explains Fischer. One advantage of the rotary table machines is the small amount of space they require, which means the distances that employees need to walk are much shorter.
In addition, the company really values ergonomics. All eight HG GRIMME machines have been equipped with acoustic enclosures. “To retain skilled staff, as well as offering good levels of pay, we also endeavour to reduce the level of noise and physical exertion,” explains Fischer.
Light barrier increases safety and working speed
Another trait that all machines have in common is that so far Fischer has also ordered a light barrier with every machine. “This speeds up the loading process and ensures occupational safety at the same time,” explains customer adviser Gehlhaar. “This is because the light barrier means that the start button only needs to be pressed once.”
The company recently acquired its sixth R-TF 1400, a 5-axis CNC rotary table milling machine for the complete machining of 3D components measuring up to 1000 mm x 800 mm x 400 mm in a single clamping assembly. The machine has remarkable travel paths of 1,040 mm x 1,400 mm x 725 mm. Fischer justified this further purchase with “four simple reasons: small amount of spaced needed for large travel paths, high machining speed, ergonomic working and excellent value for money”.
The company produces components from all customary thermoplastics that have a plate thickness of from one to ten millimetres, smooth surfaces or a pattern. “In series production, we work exclusively with 5-axis trimming,” explains the managing director. “The processing time is comparatively short. This is why the compact installation space measuring 2,700 mm x 3,500 mm x 3,500 mm and the short distances that the employees therefore have to cover are so important to us.” In the case of the rotary table machines, the workpiece is rotated, so the machining head does not have to bother travelling around the component, as is the case with a portal or gantry machine.
Even Ureol can be milled
Another advantage is the versatility: The plastics specialists regularly use the machines from the Allgäu to mill models from Ureol. They can even be used to machine workpieces made of composite materials such as CFRP or GFRP. The slender NC head has also proven its worth when it comes to machining tight cavities. The versatility is also supported by the low weight of the compact rotary table machines, which at 2.5 tonnes weigh only about as much as an average car. “As a modern company, you need to adapt to new circumstances and be flexible,” says Fischer. “We’ve changed the arrangement of the machines several times over the years. This is easy to do with a large forklift.”
Dr. Karl Gert Fischer GmbH & Co. KG in Overath-Immekeppel
5-axis trimming as standard: Fischer produces components from all customary thermoplastics that have a plate thickness of from one to ten millimetres, smooth surfaces or a pattern.
Dr. Karl Gert Fischer GmbH & Co. KG in Overath-Immekeppel (near Cologne) has developed since it was founded 50 years ago to become one of the leading suppliers of industrial thermoformed parts. The production capacity has been expanded significantly, and Fischer now caters for lots of different sectors, especially machine construction and the commercial vehicle sector.